Innovative technology is keeping pace with the increasing New Zealand forest harvest to keep forest industry workers out of harm’s way, Keith Raymond explains.
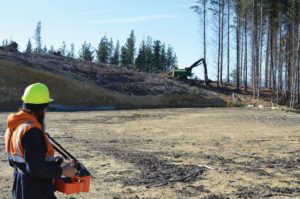
Hands off: remote control of a John Deere 909 feller buncher
Nequipment is starting to be seen out on the slopes as a result of Future Forests Research Limited’s Steepland Harvesting Primary Growth Partnership (PGP) programme.
The programme was instituted in 2010 to meet the diverse challenges of steep terrain forest harvesting that is in many ways unique to New Zealand.
Large areas of forest planted in the 1990s are reaching harvesting age from 2017 onwards and as harvesting increasingly moves into these forests on steeper land and in smaller, more isolated holdings, the challenges of maintaining international cost competitiveness and safe operations will mount.
Six years ago the New Zealand forestry sector and the Ministry for Primary Industries identified steep country harvesting as the main bottleneck to achieving greater profitability in forestry.
Worker safety is also a major issue. The forest industry has had a serious safety problem for far too long, with a long-term average fatality rate of five deaths per year and an annual serious harm injury rate of one for every 35 workers.
Tree felling and breaking out (hooking tree stems to cables) tasks have been identified as the most commonly involved in fatalities and serious harm injuries. Steep land harvesting has higher risks than harvesting on flat land, mainly due to the higher work requirements and the difficulty of operating machines on steep slopes.
Steep country forests contribute about half of New Zealand’s total annual harvest volume and, according to the industry incident reporting scheme, almost 40 percent of forestry fatalities over the last five years.
Harvesting operations on steep terrain need to keep pace with work demands and technology developments to make harvesting safer and reduce costs. Mechanisation has been seen as the solution to these problems, as it is more productive than manual operations and removes people from the hazards of tree felling and breaking out where most accidents happen.
As a result, Future Forests Research Limited (FFR) formed a Primary Growth Partnership six years ago with the Ministry for Primary Industries in steep land harvesting to realise the vision of ‘no worker on the slope, no hand on the chainsaw’.
This vision is being achieved by developing innovative harvesting technologies to realise substantial productivity gains and improve worker safety in steep terrain harvesting in New Zealand.
The Steepland Harvesting PGP programme is an alliance between the government, forest owners, engineering companies and research providers to develop equipment that will reduce cable logging costs, make harvesting jobs safer, and expand the harvesting equipment manufacturing industry.
When fully implemented the programme will reduce cable harvesting costs by 25 per cent. This will create operational savings of $8.00 per cubic metre of wood produced, and machinery sales resulting in direct economic benefits of over $128 million by 2019, as well as reducing logging injury rates.
Achievements to date
Now commencing the seventh and final year of the programme, the Forest Grower Levy Trust and FFR industry members have committed to funding the research, bringing the total industry funding in 2016/17 to $0.63 million, which will be supported by $0.42 million by the Ministry for Primary Industries to provide a funding base of $1.05 million in total.
The development work has been split into three programmes – mechanisation on steep terrain, increased productivity of cable extraction and development of operational efficiencies.
Six years down the track, there are a number of project achievements that all include elements of remote control and teleoperation:
· Alpine Grapple – a lightweight remote-operated grapple carriage CutoverCam – a remote-operated hauler vision system
· teleoperation of a John Deere feller buncher
· teleoperation of a prototype Tree-to-Tree Felling Machine Skyshifter – a remote-controlled Twin Winch Tail Hold Carriage
· a remote-controlled powered felling wedge.
A new hydraulic grapple carriage, aimed at improving grapple control, has been developed which increases the productivity of cable extraction and eliminates manual breaking out. The prototype Alpine Grapple carriage was made by Alpine Logging Ltd of South Africa, and was field tested here and modified to make it more suitable for New Zealand logging conditions.
As it is non-motorised, the Alpine Grapple has a lower capital cost, is lighter in weight and cheaper to run than conventional motorised grapples. It is suitable for running on existing two-drum cable haulers and swing yarders. The Alpine Grapple is available commercially from LogPro Limited, Alpine’s local agent, which has sold 13 units in New Zealand to date.
Breaking out in cable logging is one of the most dangerous harvesting tasks, often because the visibility of ground operations from the hauler is limited. The next product commercialised as part of the Steepland Harvesting PGP programme was the CutoverCam, an advanced hauler vision system.
This is a camera located on the cutover and linked by Internet Protocol and Wi-Fi technology to a screen in the hauler cab and streams live video of the hauler operation to the operator. With this system, the days are over of the hauler operator relying on radio and “Talkie Tooter” signals.
The hauler operator now has high resolution video coverage of the breaking out zone, and can control the camera remotely to pan from side-to-side, tilt up and down or zoom in and out to see where personnel are on the cutover before beginning the cable inhaul cycle.
This product has a very direct safety focus and has the potential to improve the productivity of cable harvesting by reducing delays in positioning cable rigging. It’s marketed by Cutover Systems Ltd in Rotorua and two units have been sold.
The initial outputs of the programme involved further developing technology which to some extent was already there, to get early gains for the industry. Over the last year some really exciting and novel products have changed the way steep terrain harvesting will be undertaken in the future. Completely new systems are being developed that include remote control and teleoperation – control beyond line of sight – of a commercial feller buncher.
A remote control system was installed into a John Deere model 909 feller buncher in 2015. The first stage of this remote-controlled tree felling project was achieved in June 2014 and the initial field testing showed promise. The application of remote control to a tracked feller buncher on steep terrain was believed to be a world first.
The next stage of the project saw the team build an operator console to teleoperate the John Deere feller buncher, so the operator can sit in comfort, outside of line of sight, and operate the machine. This full teleoperation control system was completed and installed in early July 2016 in Ross Wood’s John Deere 909 feller buncher in Nelson.
A remote control unit (RCU) was also installed in the Volvo EC290 mobile tail-hold machine in the same operation in Nelson. Three cameras have been installed in the tail-hold machine to give better vision of the tracks via the camera control and monitor installed in the hauler to enable full visibility and control of the machine from the hauler cab. Testing is now underway.
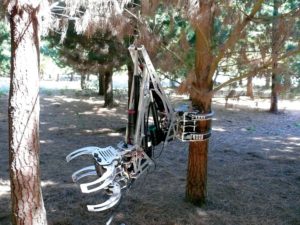
Greedy grabber: a tree-to-tree robotic felling machine prototype
Further commercialisation of the teleoperation control system is planned as part of the extension to the Steepland Harvesting PGP programme.
FFR has also been working with Scion and the University of Canterbury mechatronics programme to develop a prototype sensor- guided, bi-ped felling machine for steep country. This machine will move from tree-to-tree without touching the ground, thanks to its mechanical claws.
FFR’s ultimate objective is to combine the teleoperation control system and sophisticated sensing technology for semi-autonomous teleoperation of this robot from safe working distances, reducing risk to harvesting workers.
Proof of concept has been demonstrated, but considerable further development is needed of an applied research or engineering nature. The current prototype may be adequate for an initial market opportunity for thinning plantations or for tree measurement.
Another product of the Steepland Harvesting PGP programme is an innovative yarding carriage for remote-controlled shifting of the cable yarder skyline.
Shifting the skyline is a time-consuming, difficult and potentially hazardous task. The development of the Skyshifter Twin Winch Tail Hold Carriage by Awdon Technologies Ltd of Gisborne will enable skyline shifting to be undertaken remotely from the yarder cab.
Construction of the ‘beta prototype’ Skyshifter carriage has been completed and field tested and full production trials were successfully undertaken in July this year.
The remote-controlled felling wedge enables safer manual tree felling, improved directional felling, reduced tree breakage and improved grapple extraction productivity. The wedge will allow the faller to move away from the tree before the tree falls, thus improving safety.
Key developer Dr Paul Milliken of Cutover Systems Ltd has constructed a prototype and modifications are being made as a result of the recent production field trials.
An early adopter harvesting contractor who has ordered two manual tree-felling wedges to be converted with the remote-controlled power pack is likely to be the ‘user champion’ for the product.
Pleasing progress
These six new products are fulfilling the desired outcomes of the original Steepland Harvesting PGP business plan, to reduce harvesting costs and improve safety. Removing manual tree fallers from hazards has resulted in many contractor operations using mechanical felling now being accident-free. Where manual tree felling is still required, the remote-controlled powered felling wedge will improve safety of this operation.
Remote controlled grapple extraction has clear advantages over manual breaking out with chokers. These advantages include being very productive over short distances, and being safer by eliminating manual breaking out.
An FFR study in 2013 showed that in manually felled (unbunched) trees the productivity of the Alpine Grapple at haul distances of up to 250 metres exceeded that of the manual breaking out system by 35 percent. The cost of extraction was also lower by $3.00 per cubic metre.
The key to improving hauler productivity is bunching trees for extraction. The study found that the productivity of grapple yarding doubled compared to extracting unbunched trees with a grapple, due to 50 percent larger haul size in bunched wood.
The programme has clearly demonstrated the safety, productivity and cost advantages of mechanised felling and grapple extraction. Forest owners are starting to adopt these systems more widely, wherever terrain and safety considerations allow, as they lead to safer operations, improved hauler productivity and reduced costs.
The Steepland Harvesting PGP programme is starting to change the face of forest harvesting in New Zealand. When FFR began in 2007, there was little innovation in harvesting. Since 2010, the programme has become a catalyst to get others to think more innovatively about all aspects of tree felling and extraction.
It has catalysed a new wave of innovation in steep terrain operations. The emergence of other winch-assisted harvesters, new remote-controlled grapples with camera vision systems and GPS tracking are all examples of industry innovators seeking to modify operating techniques, improve safety and reduce the cost of harvesting, and this is a promising sign for future innovation.
One example is the development of more than 50 other traction-winch assisted machines in New Zealand. These cable-assist machines are remote-controlled and feature camera systems on the winch drums and sensor warning systems.
Over the last five years this major investment in feller bunchers and cable-assist machines by contractors has seen the level of mechanised felling, as recorded in the FFR benchmarking database, increase from 23 percent of all harvesting operations in 2009 to 38 percent in 2014, and up to 57 percent in 2015.
The use of remote-controlled grapples to mechanise cable extraction and remove manual workers from hazards, has increased, with development of other grapple carriages such as the Falcon Forestry Claw, from DC Equipment Ltd in Nelson, of which over 25 units have been sold.
A whole new area of commercial opportunity has also opened up using state-of-the-art cameras mounted to grapple carriages, winch drums and other logging equipment. Over 50 camera systems have been sold for use on logging equipment in New Zealand.
An external review of the commercialisation of FFR projects in the Steepland Harvesting PGP programme was undertaken in February this year by Geoff Todd, a commercialisation specialist from Viclink, the Victoria University technology transfer office.
Several of the recommendations from the review involved further work by FFR to engage more business development support for the various technology developers in the projects.
The Programme Steering Group for the Steepland Harvesting PGP programme supported the recommendations of the review and directed FFR to submit a proposal to the Primary Growth Partnership for a one-year extension to the Steepland Harvesting PGP programme to action these recommendations.
Drive and dedication helps an innovative concept come to fruitionThe programme extension in the 2016/17 year will focus on commercialisation of the following technology products, among others from the programme:
· the teleoperation control system
· the CutoverCam hauler vision system
· the Awdon Skyshifter tail hold carriage
· the remote-controlled powered felling wedge
The extent to which the programme has been a catalyst for changing industry practice is only starting to be realised across the industry. This programme could become a focus for improved health and safety as well as productivity improvements in the industry for many years to come.
Keith Raymond is harvesting and logistics programme manager at Future Forests Research Ltd, which was formed in 2007 by the forest industry to coordinate industry input and funding of relevant forestry research programmes
Drive and dedicatation helps an innovative project come to fruition
The successful implementation of the teleoperation concept is largely down to one man and his commitment to developing innovative tree harvesting technology.
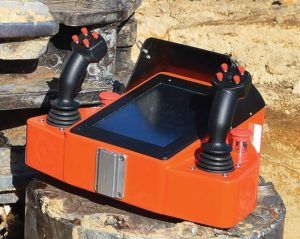
Distance driver: the remote control unit (RCU) for the John Deere 909 feller buncher
Ross Wood is one of the most respected loggers in New Zealand, given his long service to the logging industry and leadership in the development and implementation of new and exciting harvesting methods for steep slope harvesting, such as the first winch-assisted felling machine in New Zealand.
He has been operating winch-assisted feller bunchers since 2006, but he recognised that as the terrain got steeper and more challenging he needed to look at remote-control technology to give his workers a more sustainable – and safer – working environment.
Ross and his business partner Simon Rayward moved to further improve safety of harvesting operations and improve recruitment of young technically competent workers through actively by participating in the development of remote control and teleoperation technology.
They realised the potential of remote control and teleoperation of felling machines and became active partners in the Future Forests Research Ltd’s (FFR) Teleoperated Felling Machine Project, offering their John Deere 909 feller buncher to FFR for developing this teleoperation system.
The duo began by installing remote control into their John Deere 909 feller buncher last year and more recently in the installation of remote control of the Volvo 290 mobile tail hold machine. “Without this in-kind contribution this project would never have been implemented,” ffr harvesting and logistics programme manager Keith Raymond believes.
Their efforts were rewarded with the completed development of the first fully teleoperated feller buncher in New Zealand at Wood and Rayward’s Wood Contracting Nelson Ltd block in Moutere Forest, Wakefield, that is part of 32,400 ha of plantation forest originally established by Baigents of Nelson.
“Remote control of bulldozers and mining machines is common in the mining industry, but this is believed to be the first fully teleoperated tracked feller buncher in the forest industry anywhere in the world,” Raymond explains.
The successful demonstration was also due to the efforts of FFR developers Dr Paul Milliken of Cutover Systems Ltd and Daniel Lamborn and Allister Keast of ADM Design, who worked to take this project from remote control to the next step, full teleoperation (control outside line of sight).
“The aim of this project is to employ remote control and teleoperation where terrain, ground roughness or soil type limits the use of safe manned felling and bunching machine operation,” Raymond says.
The teleoperation project is a step toward FFR’s vision of “no worker on the slope, no hand on the chainsaw”, removing workers from hazardous situations.
The benefits of this project will be two-fold:
· to enable the operator to be isolated from the hazards of tree felling by providing the choice to operate the machine either in the machine cab
· or from the operator console at a remote location
· to provide opportunities for improved productivity through development of new technologies for the next stage of machine development: cabless machine designs.
Teleoperation unleashes the operator from the cab and thereby increases available operating time, Raymond notes. “Lighter weight machines with lower centre of gravity will also improve stability, reduce fuel consumption and minimise soil disturbance.”
The teleoperation project began in 2011 with feasibility assessments and some design work that included the investigation of alternatives such as “off-the- shelf” remote control systems for bulldozer applications. “However, it was decided that a New Zealand-led development project would be lower unit cost and lead to more uptake by harvesting contractors.”
Project timeline
The Teleoperation Control System project was split into two main tasks:
· teleoperation of hydraulic-over- hydraulic type machines (UC Mechatronics) and teleoperation of a John Deere 909 electric-over- hydraulic controlled machine
· development of a tree-to- tree mobility system (dubbed the “Stick Insect”).
The Task A section of the project began in three stages after the initial phases of project feasibility analysis and development planning:
· Stage 1 – develop a remote control to manage some of the functions of the John Deere 909 feller buncher within line of sight
· Stage 2 – further develop the remote control to include video feedback from one camera mounted in the cab
· Stage 3 – develop full teleoperation where the operator is sitting in a control console at the worksite in a duplicate original John Deere operator seat in front of large video monitors controlling the feller buncher outside line of sight.
Stage 1 – developing the first remote-control unit
· it was developed to NZS4240 – the New Zealand standard for remote-controlled mining equipment
· the first step was to understand the machine and method of interfacing with the electronics on the machine
· it was designed initially around machine protection
· the remote control unit (RCU) consists of two joysticks with a separate emergency stop system an aerial for communications was shielded to protect the operator
· communication monitoring ensured the link between the remote control and the machine was stable
· a controller was developed for the machine to receive messages from the remote control
· a trapped key system only allows remote control or in-cab machine operation at one time.
Stage 1 was completed in June 2014.
Stage 2 – developing video feedback
· a pan, tilt and zoom camera was installed in the feller buncher cab
· a 25-cm video display was added to the remote control unit
· the 900MHz band was selected for communication
· low video latency (delay) was applied
· machine gauges and status lights are displayed on the remote control unit.
Stage 2 was completed in June 2015.
Stage 3 – developing operator cabin and console for full teleoperation
· four cameras were installed on the feller buncher
· numerous improvements were made to the electronics
· a trailer was built and fitted out as a teleoperation console
· three large video screens were installed to provide video feedback
· audio feedback was implemented
· John Deere made an in-kind contribution of a John Deere 909 seat including joysticks and foot pedals, which was installed in the operator cabin
· safety documentation was completed for each subsystem in the Teleoperation Control System for the John Deere 909 Feller
Stage 3 was completed June 2016.