Hydraulink is a successful New Zealand business with a 75 year history, in which time it has grown to become an industry leader in hydraulic hoses, fittings, adaptors and accessories, as well as hydraulic service
Hydraulink’s rapidly expanding network now exceeds 400 service points across New Zealand, Australia and the Asia-Pacific region. The network includes branches, franchises and distributors, supported by mobile units to provide 24/7 service and safety compliance from a single contact point whenever they are needed, to prevent downtime, optimise uptime, and ensure the smooth flow of business.
And the network is continuing its expansion with the addition of new distributors and owner operators, including recent additions Byrnebuilt Engineering in Blenheim, NZ; Skiddy’s Diesel Services in Portland, Victoria; and Hydraulink North Metro Perth.
The network’s national service reach extends from growth regions such as Hamilton in New Zealand, with its diverse and expanding economic base, through to some of Australasia’s most remote energy and forestry sites, and some of its most diverse and largest mining sites.
“We are delighted to be joining the Hydraulink family, with its can-do ethos and emphasis on quality, reliable work and continued world class training and education for all its members,” said Mr Adrian Byrne, Director, Byrnebuilt Engineering.
Joel Scott, who owns his own successful Hydraulink franchise in Nelson, says making the move to a Hydraulink owner-operator was the best decision of his career.
“It was my dream to own my own business, and Hydraulink sat down with me and helped me make it work. Once I signed on, I never looked back. The customers have been really positive – I think people like to support others who get out there and do it for themselves,” said Mr Scott.
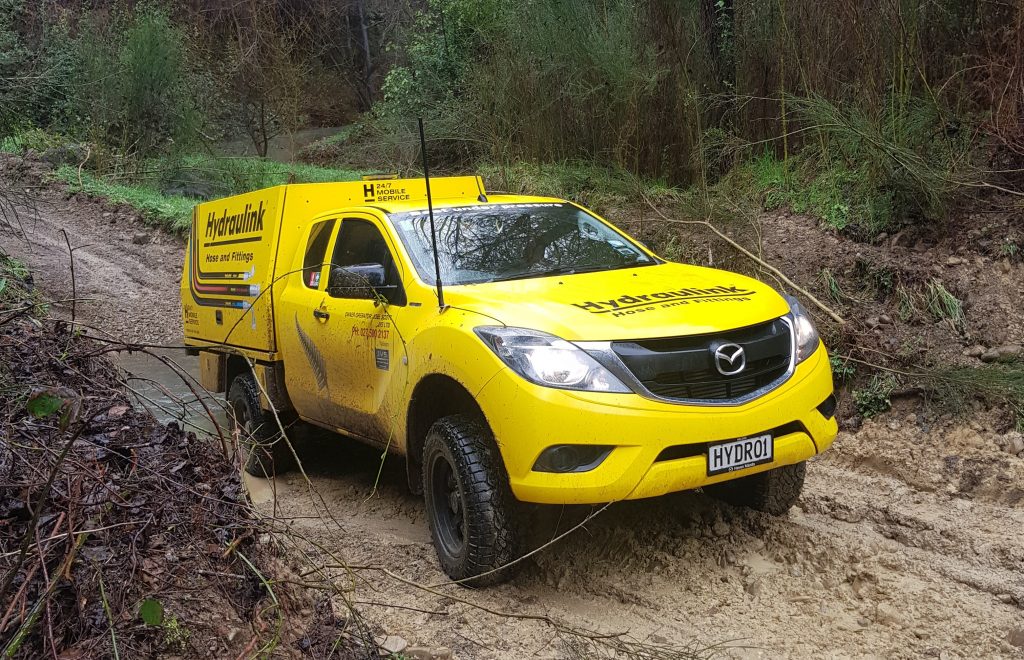
Successful Nelson NZ franchise owner Joel Scott, on his way through rough terrain to aid a digger in trouble
“Hydraulink is a good fit for us, because we are founded on the same family and service values of their franchise network, which backs its members and staff with outstanding training and resources. These help ensure proper and uniform compliance with quality and safety standards and traceability of components vital to performance and safety,” said Mr Shane Sewell, Director, Skiddys Diesel Services.
“Hydraulink has backed me all the way, because they focused you on the needs of the customers in the area in which you operate, then give you the tools, training and technology to do the job. It drives you to do better for your customer, your community and yourself, which is very rewarding,” said Mr Matt Palmer, Owner/Operator, Hydraulink North Perth Metro, whose community service with Hydraulink has included being loaned to Hydraulink New Zealand to help with rebuilding in the Kaikoura district after the earthquakes there.
Hydraulink’s expertise extends throughout a broad range of markets including:
- Roads, infrastructure, earthworks and civil engineering
- Mining, energy and oil and gas
- Agriculture and agribusiness
- Forestry
- Materials Handling, warehousing and forklifts access equipment
- Manufacturing
- Utilities and public works
- Marine
Success on both sides of the Tasman – successful NZ engineer leads new Hydraulink branch in WA
One Hydraulink operation that epitomises the company’s success on both sides of the Tasman is the new branch in Newman, Western Australia. The branch is led by Mr Kevin Ormond, whose experience includes on-site and FIFO engineering and technical work on WA mine sites, before also developing a strong and ongoing manufacturing and export business to Pilbara companies from his family’s engineering company in New Zealand.
Kevin Ormond and his family’s New Zealand and Australian interests have long been part of the Hydraulink success story as it has unfolded throughout Australasia, the Pacific and Western United States, attracting customers through its can-do ethos and investment in people, technology and training.
“The association with Hydraulink has flourished over time to become integral to how we do business. We value the strong team culture, which puts its people first. This personal commitment and the Hydraulink business model also work well for us,” said Mr Ormond, whose Dad, Vic, has assisted with the Newman setup even though he is retired.
“We saw a strong place in the market for a service-oriented hydraulic solutions provider with the local facilities to ensure customer equipment uptime is optimised and costly equipment is back in service rapidly,” said Mr Ormond.
History
Hydraulink has more than 75 years of history in providing a diverse group of customers with the hoses, fittings and services they need to keep their operations running efficiently.
It all began in 1945 with the establishment of an engineering shop in central Auckland. By 1953, the shop was manufacturing hydraulic fittings. In 1973, the Hydraulink name was adopted. Current owners Lee Short and Noel Davies purchased the business in 1989.
Today Hydraulink is a leading multi-national brand, applying its depth of experience in New Zealand, Australia and the Pacific Islands, to provide all customers with industry best practice in hose and fittings.
Advantages
“One of our big advantages at Hydraulink is that we have all this experience and capability built up under the one brand, so customers know that the excellence they receive from one branch will be the same excellence delivered to the same standards at other places. This consistency and quality is very important to customers with diverse and multiple sites who want traceability and uniformly high standards of service and safety delivered across their organisations,” says Hydraulink CEO Robin Simpson.
“The ‘can do’ attitude of our people has seen Hydraulink develop over the past 20 years to become a recognised industry leader in regional areas and across national and state borders,” he said.
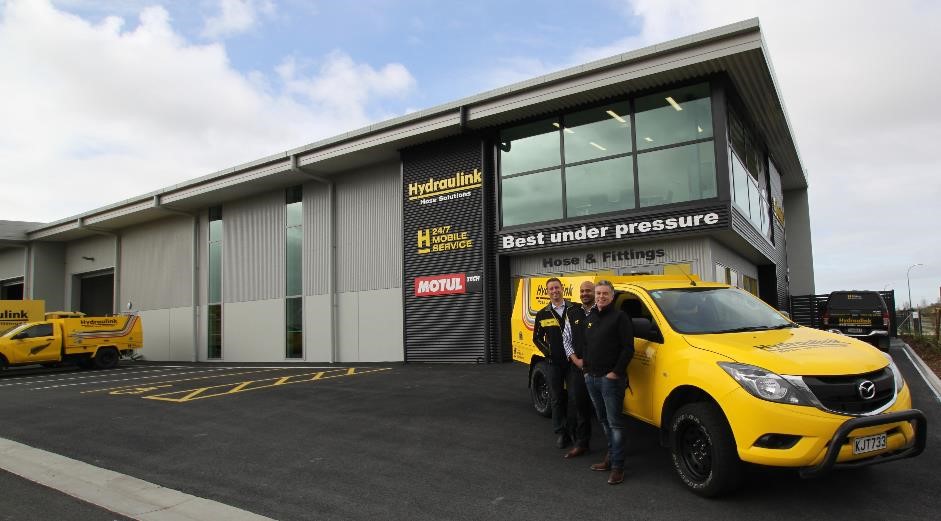
Hydraulink team members Chris Cox, National Sales and Service Manager, left, Hamilton Branch Manager Darin Pillay and CEO Robin Simpson at Hydraulink’s 800 sq m facility in Hamilton, NZ
Mr Simpson says the ongoing growth of the brand throughout Australia and New Zealand comes from strengths such as quality product and prompt expert service from the wide range of dedicated and highly skilled people who drive the company as an innovator and market leader.
Projects
Hydraulink is involved in major projects across a broad front of industries, where globally recognised companies – including major OEMs – rely on the company’s hydraulic equipment and service to minimise downtime and keep their operations running smoothly and efficiently.
Some examples include:
- OceanaGold Limited, which conducted an audit by Hydraulink Lubrication of the efficiency and reliability of Lincoln automatic lubrication systems used at their Macraes gold mine in East Otago. Additionally, over the past two years, Hydraulink has worked closely with OceanaGold’s open pit team to set up individually tailored manufacturing, stocking, supply, contamination control, health, safety and training initiatives, to provide sustainability, uptime and efficiency benefits above and beyond those previously available in New Zealand. These initiatives included:
- Enhanced levels of contamination control
- Developing a lean manufacturing process
- Developing a fit-for-purpose supply chain
- Health and safety competence training
- Queensland’s largest wind farm, the 180 MW Mt Emerald project in the State’s far north, where distributor Don Neville consistently assisted with the preparation and installation of towering turbines up to 140m tall at the tip of their blades.
- A major partnership with leading heavy machinery sales and rental specialists Porter Group, which is optimising machine reliability, uptime and safety. Central to the reliability and operation of Porter’s extensive fleet of heavy equipment and machinery is proper engineering and service of each machine’s hydraulics, including the myriad of cylinders, pistons, pumps, hoses and filters without which machinery cannot do its job. This is a role for which Porter Group has depended on Hydraulink for nearly 20 years.
- Rhomberg Rail, which is curtailing downtime and improving the maintenance productivity of its resurfacing division through the 24/7 services of hydraulic service specialist Hydraulink.
- Leading Queensland forklift company, Norlift, has received expert hydraulic engineering assistance from Hydraulink to actuate a new Rexroth joystick control for enhanced safety and efficiency of its Hyundai tyre-handling forklifts for Rio Tinto. Norlift supplied Hyundai 160D-7 forklifts, fitted with cascade tyre handlers, to Rio’s Weipa and Gove operations, which contribute the majority of the company’s 50 million tonnes of bauxite exported annually. Tyres on the vehicles used there can easily weigh more than a ton. Rio wanted a tyre-handler with better ease-of-use and safer operation, so Norlift worked with Rexroth and came up with a joystick solution, where the operator only has to move one joystick instead of the typical eight levers. Hydraulink installed all the hydraulics neatly and efficiently.
- And an extensive range of companies requiring hydraulic service, maintenance and installation, sometimes on tight deadlines or at all hours – where Hydraulink’s 24/7 availability is a major asset.
Hydraulink Academy
Hydraulink has also set up a new training academy to equip its hose centre staff, hydraulic field technicians and customers with top standards of safety and environmental practice.
The Hydraulink Academy offers a range of hydraulics-focussed training programmes. The programmes – which can be tailored to suit particular requirements – are run by qualified trainers either on-site at a customer facility, or at a dedicated Hydraulink Academy venue in New Zealand or Australia.
The initiative – which applies to Hydraulink customers and staff, as well as customers, distributors, OEMs and end-users – extends the company’s priority on investment in its staff to ensure they have an opportunity to grow with the business, while also delivering innovative solutions and consistent standards of service excellence to the advantage of customers.
Hydraulink New Zealand 0800 8066 66
Hydraulink Australia 1300 36 37 34
For further information, please contact Daniella Laurenzi, Group Marketing Manager, Australia and New Zealand, Hydraulink, 123 Long St, Smithfield NSW 2164, ph 61-2-8785 4600, Daniella.L@hydraulink.com.au.